The four linked rings are most associated with Audi today, but they originated with Auto Union. The “Union” was an agglomeration of four German companies – Audi, DKW, Horch, and Wanderer, that came together under the direction of Danish motorcycle impresario Jørgen Skafte Rasmussen in 1932.
Within five years, the name was internationally famous for its highly advanced Grand Prix cars, designed under Ferdinand Porsche and driven by the likes of Hans Stuck (Sr.) and Achille Varzi. But Auto Union was not a “make” in any real sense. The race cars had little or nothing to do with the actual consumer products the company made.
It wasn’t until a much later era, 1958, that a production car wore the Auto Union label. That car was the Auto Union 1000, our feature car today. Although nominally a new car and built well into the 1960s, the 1000 was really an update of the DKW 3=6, itself an update of the circa-1950 DKW F89.
Using the Auto Union name was an attempt to get more mileage out of what was an aging design – the car’s origins went back to 1939. War and political dislocation meant it did not appear for almost a decade, but as it happened, some of the same people who’d worked on the car in 1938 as a DKW were there to see its transition into an “Auto Union” in 1958.
It survived in part, too, thanks to the U.S. market – Daimler-Benz took over the company that very year with an eye towards selling DKWs and Auto Unions as VW rivals in the USA.
DKW and the F9
DKW was formed after J.S. Rasmussen’s college days. He’d studied in Chemnitz and stayed there afterward, setting up a factory that made steam pipe fittings in 1904.
He first tried a steam car during WW1, the Dampf-Kraft-Wagen, then produced a tiny two-stroke engine for toys – Des Knaben Wunch (the boy’s wish) – and finally, motorcycles under the DKW name, sometimes called Das Kleine Wunder (the little wonder).
The bikes were a big success and allowed Rasmussen to take over many other companies – including a small factory in Berlin’s Spandau district that was building licensed versions of the American Durant in 1928. The factory was used for DKW’s first rudimentary car, the rear-drive P-type.
The P-type wasn’t a terrible car but in cash-strapped Weimar Germany it was too expensive to be a real success. Rasmussen demanded his engineers make something simpler, cheaper, and lighter. What they came up with looked conventional but under the surface it was a real stunner.
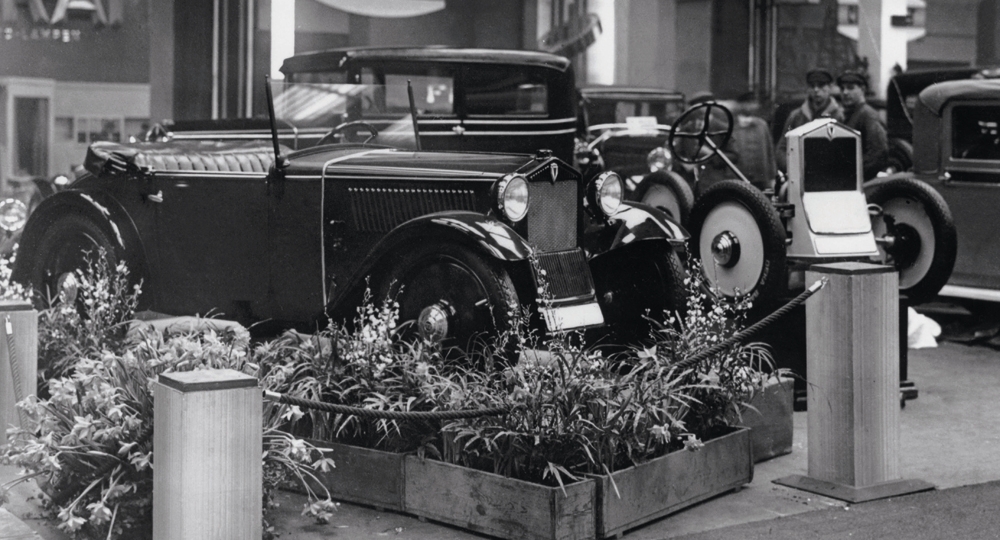
Rasmussen took the wraps off of the DKW F1 at the 1931 Berlin IAA, revealing a light, sporty looking car with front-wheel-drive and a transversely-mounted engine. This was in 1931, mind you – this sort of thinking would not be mainstream for another 25-30 years. This groundbreaking car was the very first affordable front-drive car.
The F1 used the same 584-cc two stroke as the P-type but got better gas mileage, handled better, and went faster, delivering power via Tracta joints to the front wheels and proving a good handler as a result.
It was the company’s first hit, and for the rest of the 1930s the DKW “F” models evolved, getting ever so slightly larger and more sophisticated – eventually eschewing wood frames for steel and culminating in the F8 of 1938, by then powered by either a 589-cc or a 692-cc two-stroke. Carl Hahn, Sr., the father of the future Volkswagen CEO, was DKW’s sales director, and led a strong organization.
The cars were successful and DKW expanded production to Zwickau and front drive to the Audi brand. By 1939, Auto Union’s brands had nearly 25% market share in Germany. The expansion was mostly driven by Dr. Hahn, who had a GM-like vision for Auto Union, with DKW the entry level, Audi and Wanderer the sort of Olds and Buick, and Horch at the top. Newer models after 1936 were meant to complement each other.
Even before the F8 was launched, DKW’s engineers were working on a much more advanced car. With the front-drive, two-stroke formula more or less perfected, the design emphasis on what would be the prospective “F9” was on creating a very advanced, aerodynamic car, now with three cylinders, that would be much faster and quieter.
Hitler’s Volkswagen would soon arrive and severely undercut DKW’s low-end products. There was no stopping that project, so DKW would have to do new things – and the “F9” was the first step. Technical director William Werner oversaw the project. Werner, American born but living in Germany since he was a teenager, was the force behind many of Auto Union’s advanced car projects. He left the company after the war, but his role in the F9 and its descendants was not over.
Body engineer Albert Locke led the program to develop the aerodynamic shell, which was styled mostly by Günter Mickwausch, who had come to Auto Union via Horch. Mickwausch had created many bodies for Horch in the 1930s and the form of the F9 would be futuristic and flowing. He worked with modeler Wilhelm Bohm and aerodynamicist Wunibald Kamm was consulted on the project.
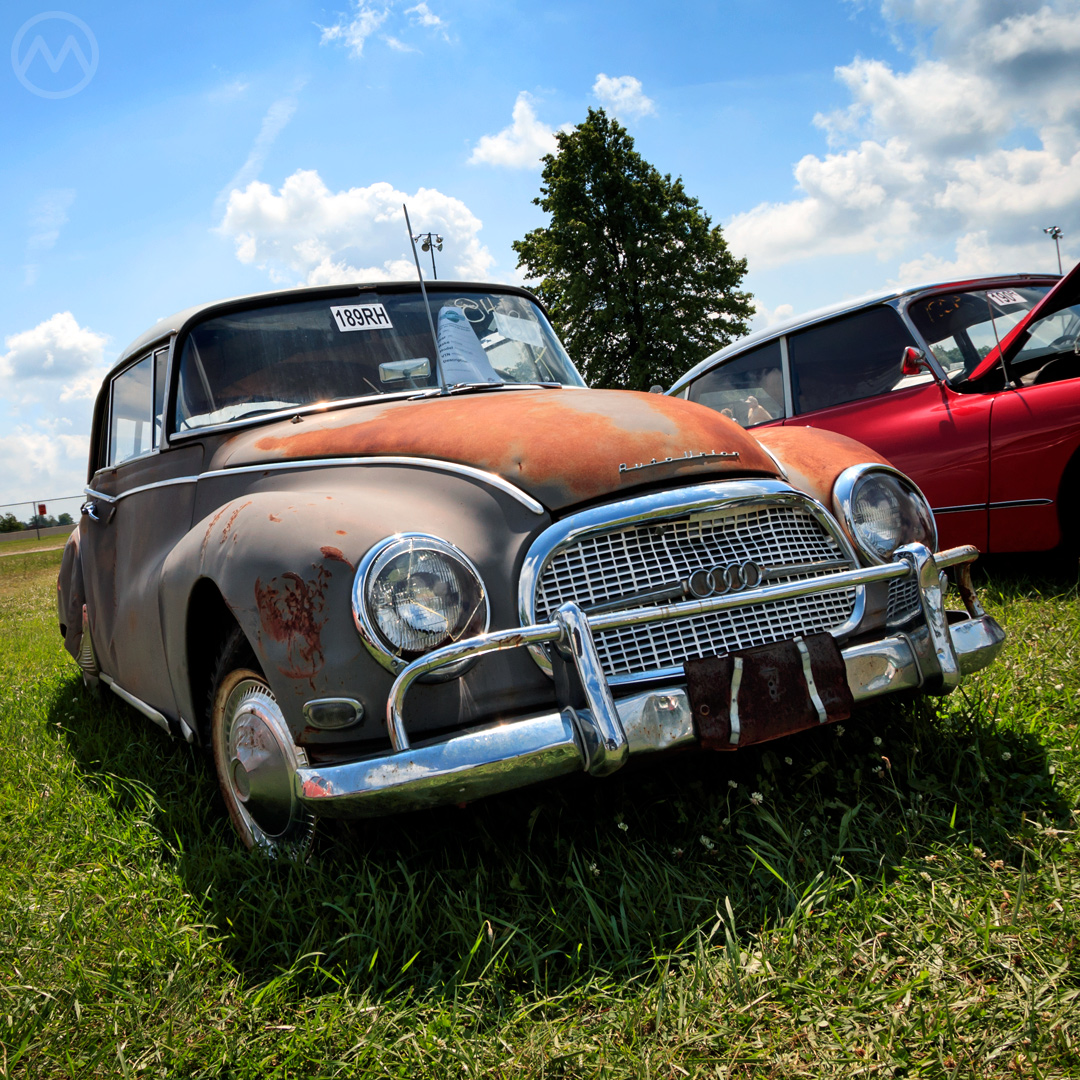
Nor was it the only advanced Auto Union prototype of the time – the Horch 930S, shown in 1939 but never built, was similarly aerodynamic.
F9 prototypes were up and running in 1939 and the car theoretically slated for a 1940 introduction when the war began. Plans to tool up for the car were soon put on ice and DKW built F8s until 1942, when all civilian car production was stopped in favor of building war material.
The Red Army
In 1930, when DKW was struggling with the P-type, one of its creditors – Sächsische Staatsbank – had mandated the appointment of Dr. Richard Bruhn to the board. After the Auto Union merger, Rasmussen and Bruhn clashed often and intensely. Rasmussen, who had built the entire company, quit in 1934. While Hahn ran the car side of things after that, Bruhn ran the company.
Bruhn, with close political ties to the Nazis, shepherded the company thereafter – including during the war when it heavily used slave labor. The company’s factories were repeatedly bombed during the later stages of the war, with the Wanderer factory completely destroyed. The Americans liberated Zwickau and Chemnitz, but the cities were to fall under the Soviet zone of occupation after the Potsdam conference.
Bruhn, despite being detained for a time and having to undergo denazification, fled to Bavaria in the American zone. So did lots of other Auto Union execs and employees, who took a dim view of a potential life under Soviet control. Some who stayed were imprisoned by the Soviets until 1950.
The factories were now lost and many of the machine tools appropriated. What remained in the east became part of IFA – Industrieverband Fahrzeugbau – the East German state-owned umbrella company for automobile and truck production.
DKWs had been popular cars before the war and being cheap and durable, many survived – Bruhn and his group of former employees established a parts and service operation in Ingolstadt, cooperating with the smaller former parts and service pieces of Auto Union that were located in the western zones.
They got control of the DKW and Auto Union names in the long process of setting up the new company, during which they acknowledged that their company was something of a “pirate” operation. But with the east in chaos, there was nobody to stop them and they did have some help from former coworkers still in the east – IFA wasn’t even organized yet.
With the help of Marshall Plan and the help of banker Friedrich Carl von Oppenheim, this “Central depot” became the “new” Auto Union in 1949 – Auto Union Gmbh, where the old one was still operating as Auto Union AG.
Although Hahn played a big role in restarting the company, much of this activity was organized by Bruhn, without whom the company would not have been reborn, but it was a problematic legacy. In the interest of re-establishing organized society and putting people to work, Bruhn’s past associations were glossed over until the 21st century.
The operation ran first from a converted granary, but once they had enough capital the new company bought a damaged factory in Düsseldorf from munitions maker Rhinemetall-Borsig, refitted it, and restarted production of DKW cars in 1950. Actually, trucks – their first product was the Schnellaster van, at Ingolstadt.
Before the war, orders had been placed for tooling at some firms now in the western zone, and as a result, much of the technology needed to make the F9 was available on both sides of the division and the company retained the old Spandau facility where parts could be made, so production of a DKW car (at Düsseldorf) was not so difficult to resume.
The Schnellaster was built on the design pieces needed to complete the car, and came first because commercial vehicles were in demand.
The new DKW car was directly based on the F9 prototype and called the DKW F89 or Meisterklasse, reviving a 1930s name. In Zwickau, IFA released the F9 as it was intended in 1940, with its new three-cylinder engine. At DKW, the F89 had to make due to the F8’s older twin as Ingolstadt didn’t have the ability to finish up the triple on its own in time to release the car.
This led to the odd situation of two separate companies selling what was essentially the same car – both the F9 and F89 were closely based on Mickwausch’s F9 prototypes, but in this rare instance the Socialist version was the better car thanks to its additional power. Contemporary accounts suggest it was more reliable, too.
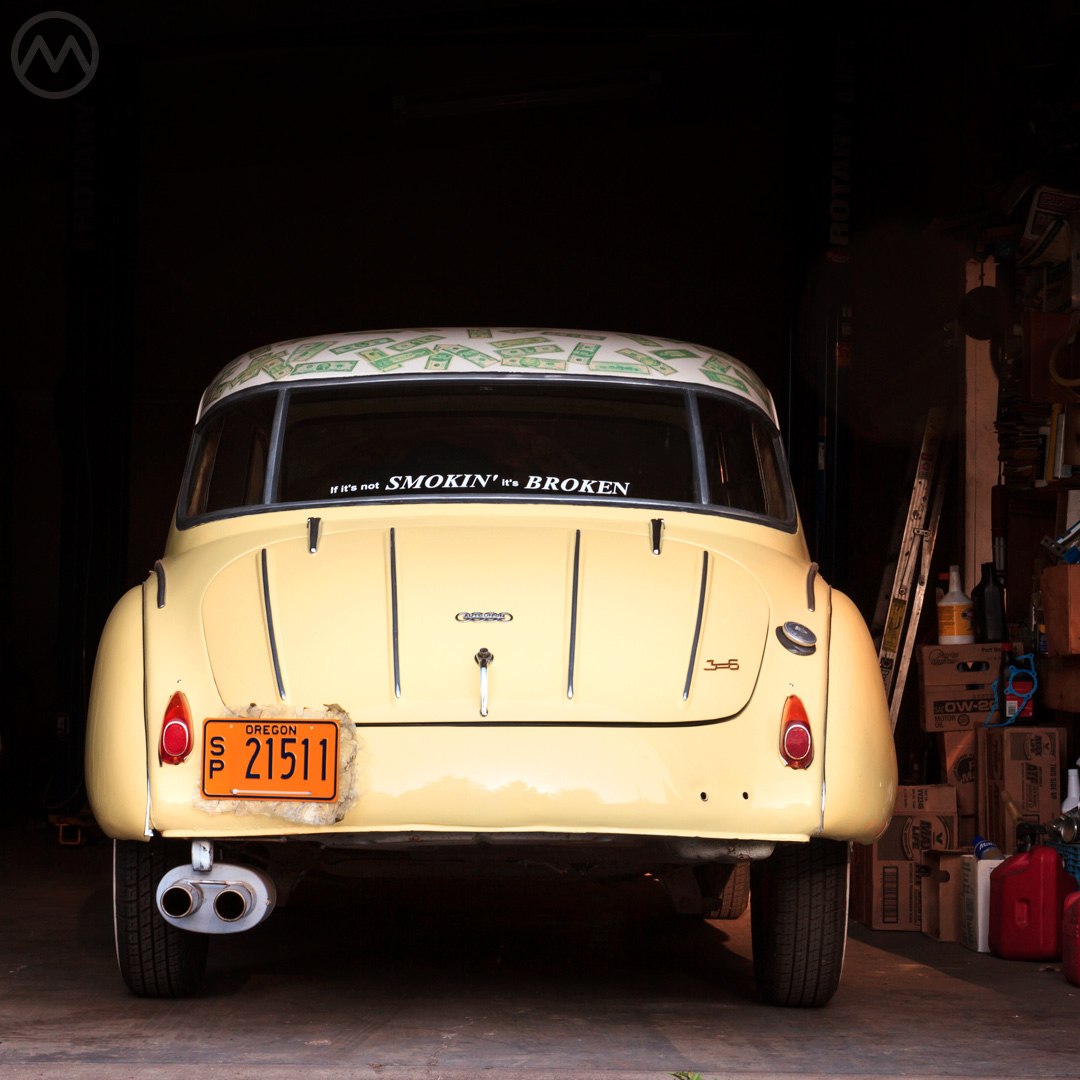
Two-strokes deliver a punch for their size, and the IFA F9 delivered 30 hp from 910cc, the F89 23 hp from 684-cc. The aerodynamic body gave it good stability at high speed – which was also true of the DKW – but the IFA was lighter and faster in every respect, and no worse on gas.
The next step was for DKW to engineer a triple of its own, which is exactly what happened in 1953-54 when the F89 was redesigned into the Sonderklasse (another old DKW name) or F91.
3=6 to 1000
The Sonderklasse, reviving a prewar name from one of the earlier F-series DKWs, was cosmetically almost no different from the F89. The shell had been modern in 1950 even if the running gear was not – and now that was updated. Engineering updates were done under the eye of Kurt Schwenk, who had designed the Schnellaster van and was working on a variety of advanced projects including a newer, smaller DKW with a plastic body.
The triple, now mounted longitudinally, produced 34hp from 894-cc and eventually a four-speed soon became an option (the F89 and early F91s had been three-speeders). The car was appreciably faster and generally had nicer equipment levels, too.
The car was a success and DKW took every opportunity to market its new power – that’s where 3=6 came from. At first 3=6 was just a badge and a marketing slogan, but eventually that became the actual name in some markets.
Because of the power of the two stroke from such a small displacement, DKW advertised it as being equal to a four-stroke six-cylinder engine. That was a bit of a stretch, but it wasn’t a slow car by small car standards in 1953-54 and the Sonderklasse had a spectacular competition record – for its size, it was hard to beat.
In 1940, the F9 would have been among a group of cutting edge, streamlined Germany cars including the Hanomag 1.3 (which partially inspired the Volvo PV444), the Volkswagen, and the “Autobahn” Adler 2.5. By 1955 it was beginning to look a little old. A pretty hardtop coupe was added in 1953, which helped, but the car was still clearly from a past era and from 1955 sales began to soften.
DKW responded first by slightly stretching and widening it into the update F93, now with a larger four-door sedan option, and by marketing an exciting little sports car variant – the Monza – designed in part by ex-Porsche man Robert Eberan von Eberhorst.
That was not really enough for DKW dealers, who were continuing to see an exodus to other brands. In the early 1950s Schwenk had championed the protracted development of a potential new car called the Auto Union FX, an ambitious plastic-bodied car that went nowhere and dragged on into 1955. Major investor Karl Friedrich Flick disliked the plastic car, and management worried buyers would not trust its crashworthiness.
Bruhn still wanted something that could take on VW and that just wasn’t possible with the FX. William Werner returned in mid-1956 at the insistence of major shareholder Karl Flick. Eberhorst, more interested in racing than production cars, and Schwenk, blamed for the failure of the FX, were soon relieved of duty. Schwenk went to Ford to work on the Taunus, and later to VW.
The Auto Union 1000S
The long-delayed small car project had sapped most of Auto Union’s finances while a flotilla of new small cars came on the German market – mostly microcars. Meanwhile the Vespa had destroyed DKW’s small, cheap motorcycle business. Auto Union’s dealers and major shareholders, Oppenheim and Flick – were impatient.
After that, Flick became much more of an activist investor and his demands were carried out through Werner. Bruhn and Hahn, now old men, retired and strategies began to shift.
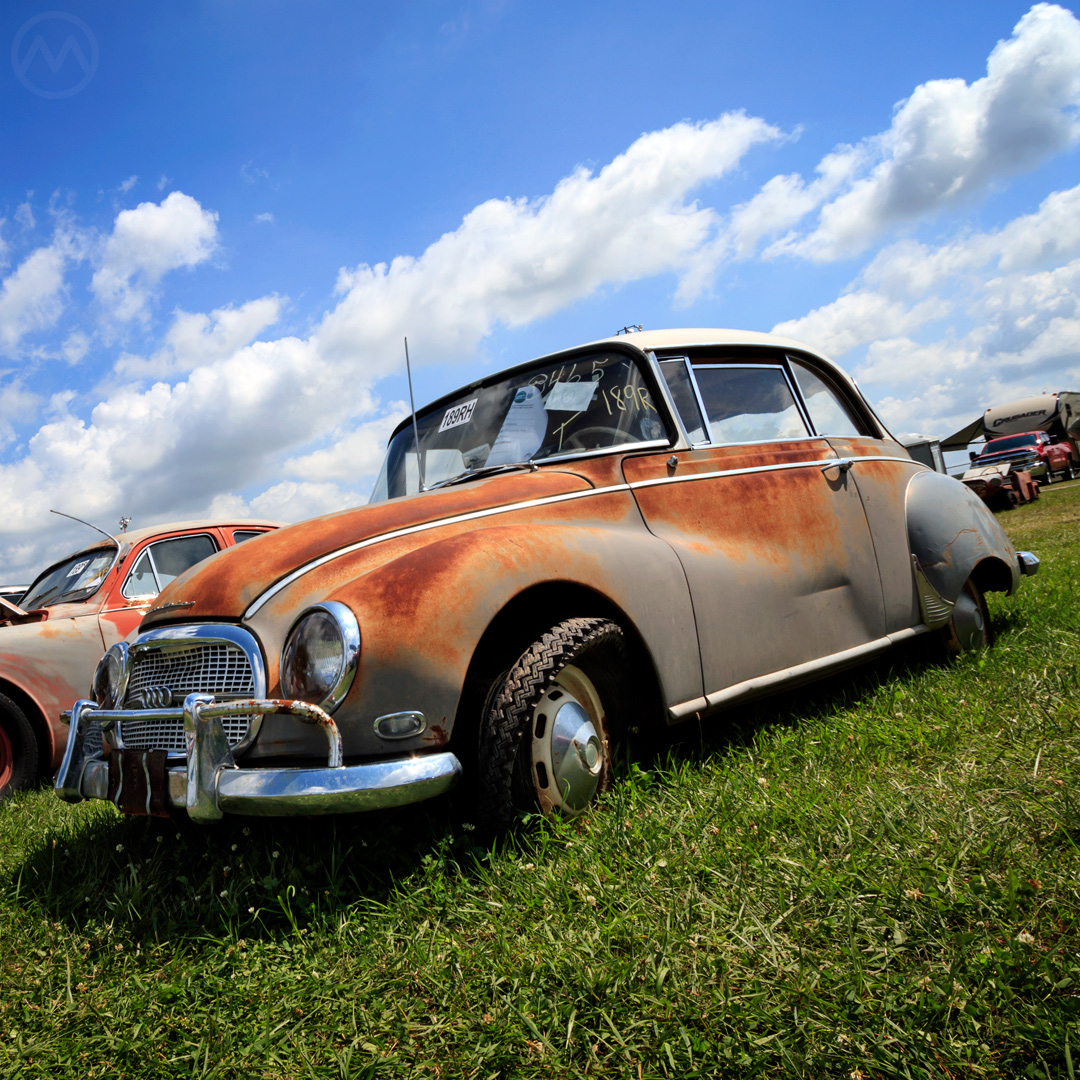
Werner was tasked by Oppenheim with coming up with a new small car, which became the DKW Junior. It was designed in a hurry, but it looked quite modern in 1957, and that was what dealers (and shareholders) wanted to see. It was not, however, quite ready for production at that time, nor did Auto Union have the funds to build it – roughly 40-60 Million DM at the time.
This situation was made more embarrassing by the fact that the Eastern Zwickau plant was now building a cheap small car with a body made of plastic – the AWZ/Sachsenring P70. Flick and the other investors began looking for a buyer, but Auto Union still had to keep making cars to generate cash flow.
To keep the F9-based designs alive, a new strategy was devised – gild the lily. The 3=6 would give way to an evolutionary car under the Auto Union label, which might seem more upmarket than DKW. It would have more power, more features, and be marketed as more of a premium car. Following on from the publicity-generating Monza, there would be a coachbuilt sports car version with lines inspired by the Ford Thunderbird (which Werner had fallen for on a trip to the USA in 1955).
The Auto Union 1000 was released in 1958, although the 3=6 remained in production alongside it for some months, as the DKW 900. Early on, the changes from “DKW” to “Auto Union” consisted mostly of the engine change and the badges, but in the summer of 1959 the car was updated with a wraparound windshield and slightly updated styling, courtesy of the company’s new stylist Josef Dienst.
The car now featured a 981-cc triple with up to 55hp, though most versions were in the 45-50 hp range. That was a big increase over the old 34-hp 3=6 and the cars were faster than ever. They were plusher too, with more equipment and fancier trim added. They clearly resembled what had come before, but they were the best of the line.
The car arrived just as Flick maneuvered finances, backed in part by Bayerische Staatsbank, to sell Auto Union to Daimler-Benz. Starting in late 1957, Daimler gradually acquired 100% of Auto Union by the summer of 1958.
Your Studebaker-Mercedes-Auto Union Dealer
During the shift, Werner continued to push the development of the DKW Junior, which finally saw production in 1959. The motorcycle division was sold off and production was consolidated to Ingolstadt – Düsseldorf became a Mercedes facility.
Although Daimler was skeptical of the purchase of Auto Union, it wanted DKW as an affordable brand for the purpose of breaking into the U.S. market. DKW already had a foothold in the USA though its presence was small – about 2-3,000 units a year were sold through distributors in California and Connecticut.
Daimler, eyeing Volkswagen’s success, reasoned that it could expand its own presence considerably if it had more affordable cars to sell, and that’s where the Auto Union/DKW cars came in. Daimler already had a distribution agreement with Studebaker, who themselves were looking for any way possible to get buyers into the store.
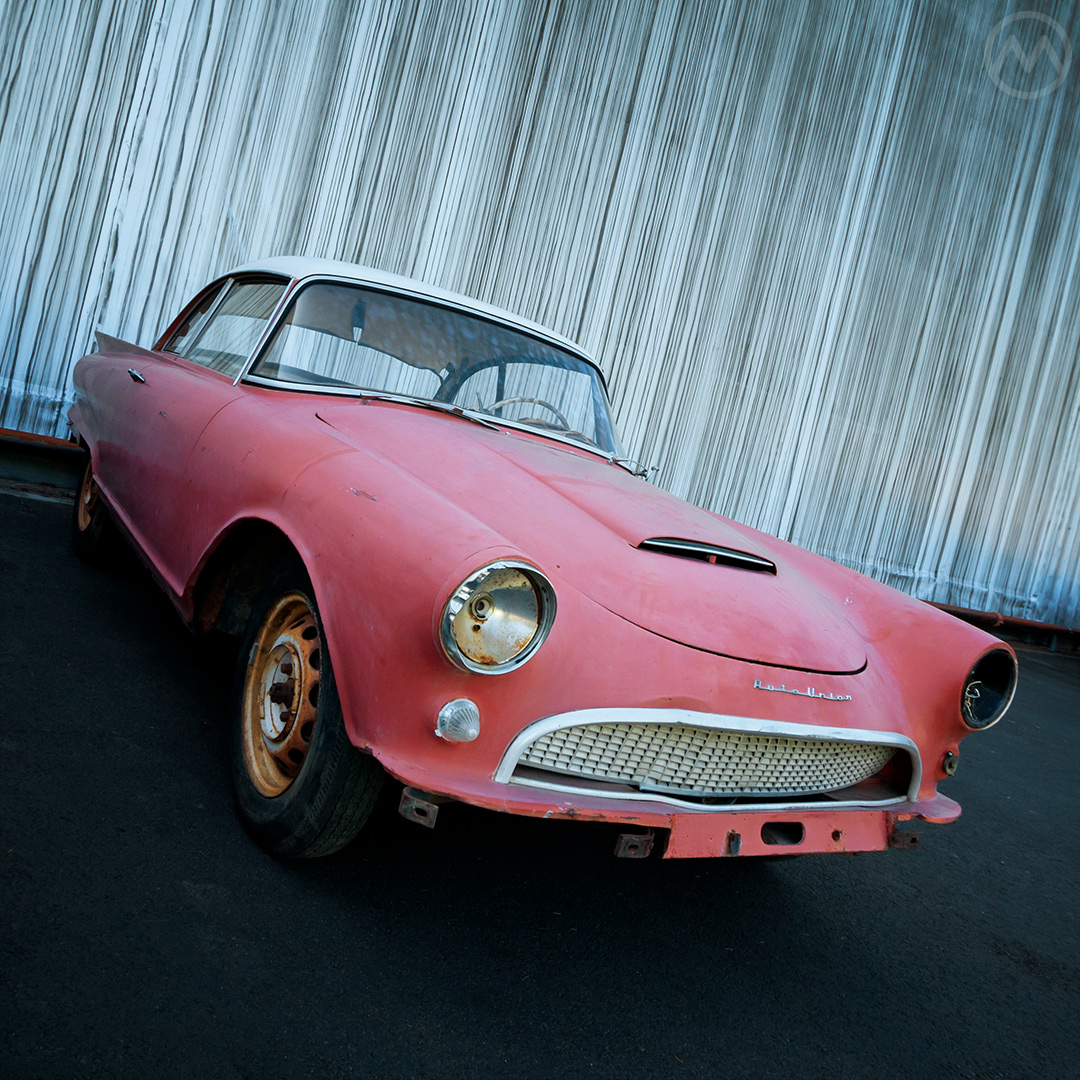
This plan might have worked better if the Auto Union sourced cars had used four-stroke engines. The United States didn’t have a long tradition of cheap two-stroke cars like Germany, and there was some resistance to the practicalities of having to mix oil and gas, and to the potential for smoke and noise, both greater than on conventional four-stroke cars.
The 1000S was a good car to drive, however, and got high marks for its performance compared to other 1-liter European cars, in part because of the two-stroke punch.
The move was also ill-timed. The Junior, which is the car that Daimler had hoped would carry its efforts, arrived in 1959 – just in time for the market for foreign small cars to be hit hard by Detroit’s compacts. The 1000S, while a nice car, wasn’t particularly cheap – for the same money a buyer could saddle up with a Chevy Bel Air.
Of more interest to Americans was the 1000SP – the miniature German T-bird built by Baur atop the 1000S mechanicals, but it cost $3,900 – as much as a Corvette. DKW and Auto Union sales remained pretty much at their 1950s levels even after the Studebaker connection, though Mercedes was able to expand its presence via the agreement.
Daimler’s experiment with DKW and Auto Union proved to be a money loser although the Auto Unions were fairly good sellers at home for such an old car – 171,000 were made from 1958 to 1963 plus about 6,000 SPs.
The Studebaker distribution agreement was terminated early, in 1964, the same year Daimler sold Auto Union to Volkswagen, where the remnants became the modern Audi brand. DKW and Auto Union were phased out because of their association with two-strokes, which in the 1960s continued to encounter more resistance from customers.
The F9 based cars had an afterlife in South America, where Auto Union had a strong licensed presence, and remained in production in Brazil until 1967 and in Argentina until 1969.